Ultrapure Water Close System into Semiconductor Plant
cut lineAbstract
The features of a ultra pure water supply system demanded by semiconductor plants are not only a high purity of water, but also low cost, energy saving, resource saving, resource recycling, space saving and low maintenance. To meet these demands, we installed an ultra pure water closed system in Oki’s semiconductor plants. This pure water supply equipment supplies ultra pure water with a 95% or higher pure water recovery percentage. The waste water collection equipment has a low pressure evaporation condenser, which saved energy, resources and space. Waste water treatment equipment can recycle high purity calcium fluoride (fluorite) using a hydrofluoric acid recycling unit with a high efficiency substitution reaction, which allows hydrofluoric acid material to be recycled. The running costs are about double that of a semi-closed system, which has a recovery percentage of 80%.
1. Introduction
Recently ozone sphere protection, global warming controls and resources exhaustion control measures are attracting attention as global scale environmental problems. For the purpose of preventing global environment pollution, the health of employees and safety controls, announcements subjected to waste control measures, energy saving and safety and sanitation are continuing from manufacturers inside and outside Japan.
For semiconductor manufacturing plants as well, the construction of clean and stable operations with environmental protection measures is critical, not just constructing facilities that decrease operations costs. Ultrapure water manufacturing systems are necessary to make wafer surfaces ultra clean, but the expenses to manufacture ultra pure water and to treat waste water are high. Figure 1 shows a breakdown of the construction costs of a facility at an Oki semiconductor manufacturing plant. The construction costs required to construct an ultra pure water and waste water treatment systems make up about 15% of the entire facility.
Oki has been working on the commercialization of an ultra pure water closed system for mass production plants, to meet demands for total costs reduction, including construction and operation costs, and for environmental protection, aiming at increasing the purity of ultra pure water quality, improving the efficiency of operations, and making processing functions higher in an ultra pure water manufacturing system. Thus far we have been using an ultra pure water semi-closed system with an 80% recovery ratio, but we decided to adopt an ultra pure water closed system for the latest semiconductor plants, because water utilization efficiency can be improved. This decision is based on cost reduction, the effective use of space, and environmental protection. To make this ultra pure water system completely closed, we targeted a pure water recover ratio of 95% or more, total organic carbon (TOC) concentration of pure water quality of 1 ppb or less, and a recovered calcium fluoride (Ca2F ) purity at 92% or more.
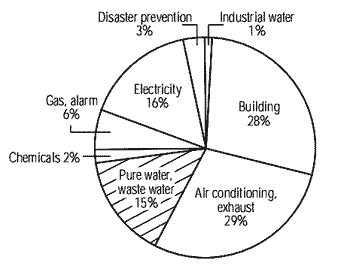
Figure 1: Breakdown of construction costs of semiconductor plant
This paper describes the current operation status of ultra pure water closed systems at the latest semiconductor mass production plants. In particular, (1) the performance and quality of ultra pure water supply systems, the recovery treatment systems and waste water treatment systems, (2) the performance of evaporative concentrations and recovery systems aiming at environmental protection, and (3) the performance of hydrofluoric acid recovery systems aiming at recycling resources is described. Finally, Oki’s approach to costs reduction and handling environmental problems in the future are described.
2. Current operation status of ultra purewater closed systems
2.1 Overview of closed systems
Photo 1 shows a panoramic view of the facility yard at an Oki semiconductor plant. Figure 2 shows the configuration of an ultra pure water closed system and the processing flow. This system uses industrial water as the raw water, and consists of an ultra pure water supply system (pre-treatment system, primary pure water system, secondary pure water system), a recovery system to recover pure water used at the usage point (dilution line recovery system, concentration line recovery system), an evaporative concentration recovery system, an hydrofluoric acid recovery system, an alkali line waste water treatment system, an IPA (isopropyl alcohol) waste water treatment system, and a backgrind waste water recovery system. These systems have resoiling prevention measures considering quality stability. Materials / components used are of high purity and have a minimal dissolution of contaminants.
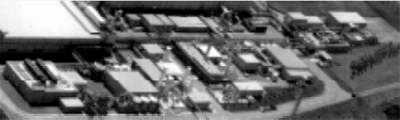
Photo 1: Panoramic view of facility yard for semiconductor plant
Impurities contained in recovered raw water vary. For example, metallic ion (inorganic ion, heavy metal ion), organic matter (TOC: Total Organic Carbon), particles, colloidal silica (SiO2), microbes and bacteria. These impurities can be removed by combining systems that have various impurities removal functions (coagulation filtration, membrane separation, ion exchange, ultra violet sterilization, degassing, biological processing, evaporative concentration, substituted reaction systems, etc.).
Figure 2: Treatment flow of ultra pure water closed system
Figure 3 shows a comparison of the running costs of an ultra pure water closed system between the design target and current status. The running costs of the current closed system is about 70% of the design target. This running costs is about double that of a semi-closed system (pure water recover ratio: 80%).
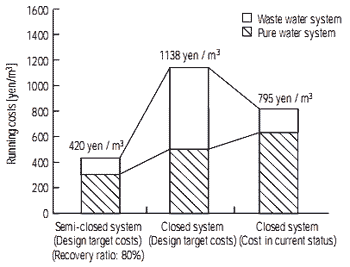
Figure 3: Comparison of system running costs between design and current status
2.2 Performance of ultra pure water supply system
Quality control items for ultra pure water currently required for a semiconductor manufacturing plant are resistivity, TOC, heavy metal ion, silica, dissolved oxygen and others. It is important to maintain the impurities concentration to an extremely low level in the beginning of operations. Figure 4 shows the changes in resistivity at UF (Ultra Filtration) of a secondary pure water system when the production system begins operations. Figure 5 shows the change of TOC concentration. Resistivity was maintained to almost the same as the theoretical value of 18.24MΩ • cm. The TOC concentration was maintained to be 1 µg/l (1 ppb) or less. This closed system can supply high purity and high quality ultra pure water to the usage points from an operation start status. A vertical startup, which achieves target control values at the beginning of operations, is possible. We also confirmed that the electric characteristics, including the withstand voltage of oxide film and carrier life times related to the reliability of semiconductor devices, are improved by cleaning wafer surfaces with this ultra pure water. Wafer surfaces were cleaned to ultra clean without contamination by supplying such high quality ultra pure water to the wafer process, and a high quality and high yield of semiconductor devices were implemented.
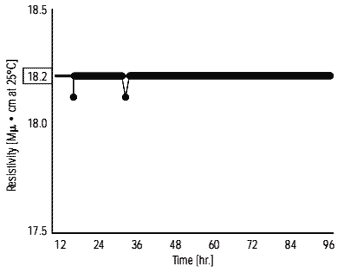
Figure 4: Change of resistivity at UF outlet of secondary pure water system
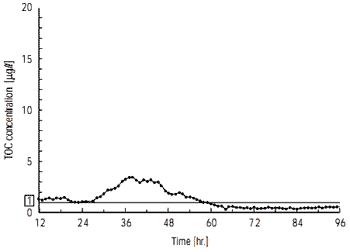
Figure 5: Change of TOC concentration at UF outlet of secondary pure water system
2.3 Performance of recovery system
We considered water utilization efficiency in the entire plant when we decided how to reuse recovered water. The recovery system implemented about 95% of pure water recovery ratio, including dilution lines and concentration lines, mostly for acid and alkali lines. This recovery ratio became possible because the system was designed such that waste liquid from the usage points can be recovered according to type and concentration. To control pollution at the entrance of the recovery system, safety measures are taken by an in-line monitor, which insures stable water quality.
2.4 Performance of waste water treatment system
This section describes the evaporative concentration recovery system and hydrofluoric acid recovery system of the waste water treatment system, which supports environmental protection and resource recycling.
Figure 6 shows the processing flow of the evaporative concentration recovery system. In this system, vacuum processing type steam compression evaporation equipment and an ammonia (NH4) removal tower efficiently removes ammonia ions, and the treated water is reused as facility water. Because of vacuum type processing, this system can reduce power and steam consumption. In this way the system contributes to global environmental protection by saving energy, saving resources and saving space.
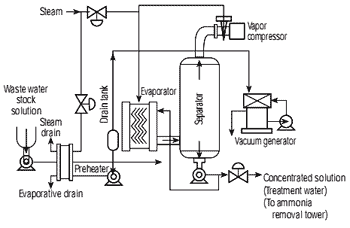
Figure 6: Treatment flow of evaporative concentration recovery system
Figure 7 shows the processing flow of the hydrofluoric acid recovery system. This system has a 99% or higher fluorine removal ratio, which is higher than the value acquired at an experimental plant (fluorine remove: 92%), and can generate high purity calcium fluoride (CaF2). This is because a substituted reaction method using granular calcium carbonate was adopted. The structure of the reaction tower, which can make high efficient substituted reaction possible, reduces the consumption of the granular calcium carbonate. In this way we confirmed that this recovery system, which was technically established in experimental plants, has a high reliability which allows the actual use of the system in mass production plants.
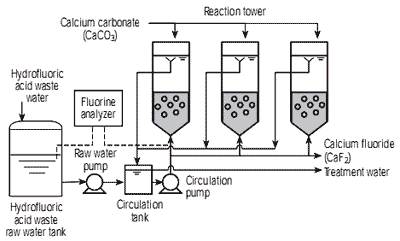
Figure 7: Treatment flow of hydrofluoric acid recovery system
Table 1 shows a comparison of the purity of CaF2 regenerated in experimental plants and mass production plants. CaF2 regenerated in a mass production plant has a 97.7% purity. This indicates that the potential of recycling CaF2 was verified in an actual mass production plant, and makes it possible to reduce the mining of mineral resources for businesses (such as hydrofluoric acid manufacturing industries) that use fluorite (CaF2) as a raw material and, therefore, saves resources.
Content (%) | ||
Component | Experimental plant | Mass production plant |
CaF2 | 92 | 97.7 |
CaCO3 | 5 | 0.37 |
SiO2 | <5 | 0.64 |
Table 1: Comparison of purity of recovered CaF2
3. Conclusion
We installed an ultra pure water closed system in an Oki semiconductor manufacturing plant. This paper presented an overview of this system and described its features and performance. This closed system implemented a pure water recovery ratio of 95% or more, and a TOC of 1 ppb or less as the pure water quality at the usage points, and recovered CaF2 with a 97% or higher purity. These results indicate that the established ultra pure water closed system is effective in terms of low costs, environmental protection, saving resources and in recycling. In the future, we will consider adopting ultra low pressure RO (Reverse Osmosis), large UF (Ultra Filtration), the recycling of industrial waste and other matters to improve the facility aiming at high quality, stable supply and maintenance savings. It is also important to establish a facility that does not fluctuate and is completely parameter-controlled, for ultra pure water quality used at usage points, so that ultra pure water can flexibly support target semiconductor device quality. We would like to work on the establishment of future semiconductor plant facilities to support semiconductor device quality based on the “gentle to the earth, gentle to humans” expression.